Recyclage plastique
Le recyclage chimique des déchets plastiques est devenu de plus en plus important ces dernières années. La société Ekato apporte sa pierre à l’édifice et contribue, grâce à ses solutions sur mesure, à l’économie circulaire. Nous vous partageons ici l’étude menée par Ekato, qui met en lumière les besoins actuels et les solutions à appliquer.
Plus de huit milliards de tonnes de plastique ont été produites dans le monde au cours des 70 dernières années, la plupart depuis le début des années 2000. À titre d’exemple, selon l’Agence fédérale allemande pour l’environnement, chaque allemand produit environ 108 kilogrammes de déchets d’emballage par an, une quantité qui ne cesse d’augmenter. Les déchets plastiques sont désormais un problème environnemental mondial. Malheureusement, c’est le cas d’une grande majorité des produits polymères: quelle que soit la forme sous laquelle ils sont introduits dans la nature, leur dégradation dans les conditions atmosphériques est, au mieux extrêmement faible, au pire inexistante. C’est une réelle mise en danger de l’environnement et particulièrement des océans. Nous avons tous en tête les images des « îles de plastique » apparues dans des proportions inimaginables dans le Pacifique Nord et Sud. Ce défi planétaire fait du recyclage des plastiques une des préoccupations majeures du grand public. L’objectif devrait être une « économie circulaire », c’est-à-dire, dans l’idéal, un cycle mondial fermé des matières plastiques.
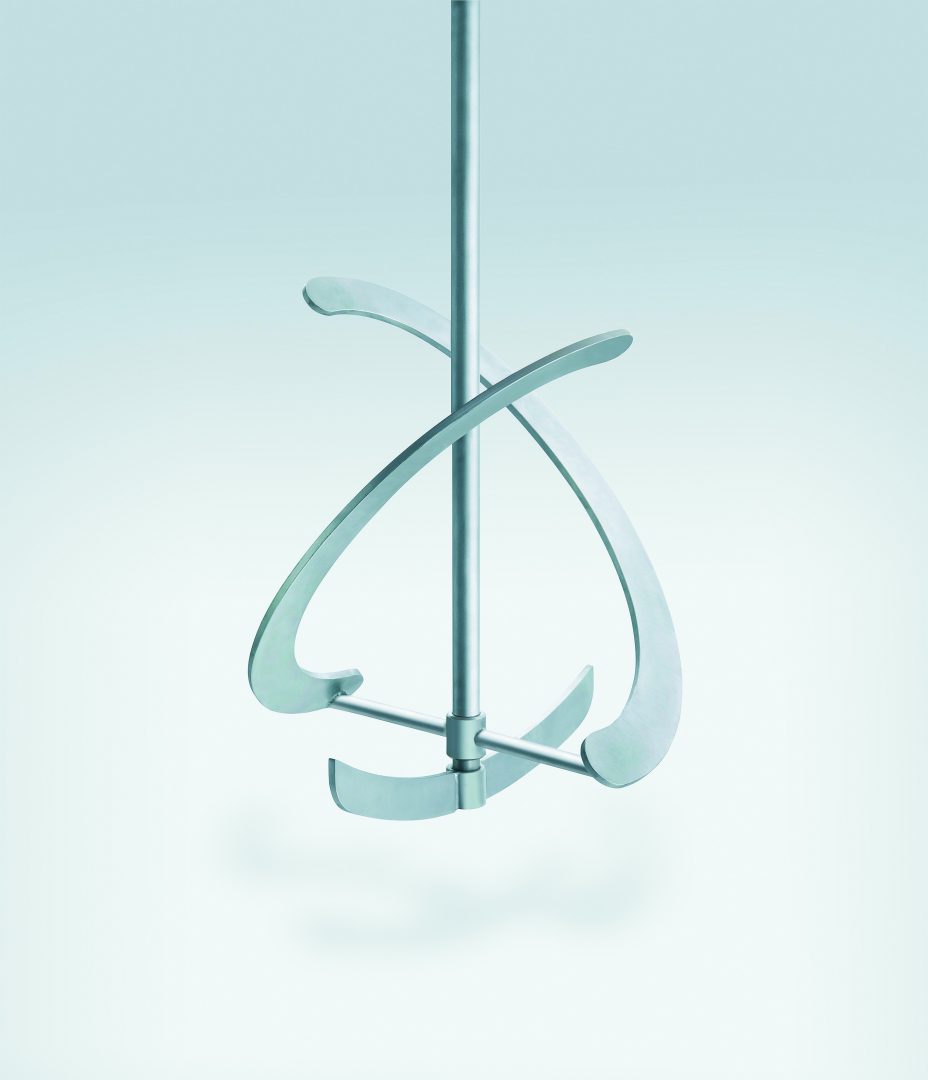
La nécessité de solutions performantes
Actuellement, le recyclage est principalement effectué à l’aide de procédés mécaniques : les déchets plastiques sont triés en fonction du type de plastique, puis lavés, fondus et transformés en produits dits recyclés. Ces produits recyclés remplacent l’utilisation de nouvelles matières plastiques à base de matières premières fossiles et permettent de réduire les émissions de CO2. Lors du recyclage mécanique, la structure chimique des plastiques est conservée. Ce recyclage mécanique des déchets plastiques, très courant pour les bouteilles en PET, atteint ses limites lorsque le matériau de départ est contaminé ou d’un type différent. Pour se rapprocher significativement de l’objectif d’une « économie du plastique circulaire », des solutions plus sophistiquées sont nécessaires. Les fractions de déchets plastiques les plus importantes et les plus répandues, par exemple le contenu des sacs jaunes ou des poubelles jaunes contiennent de nombreuses impuretés, des métaux, des additifs, des colorants ou des films multicouches. Pour réussir à réintroduire ces fractions mixtes dans un cycle, des processus de recyclage mécanique et chimique doivent être mis en place à grande échelle.
Les procédés de recyclage chimique en pratique
Certains procédés chimiques permettent déjà de récupérer des matières premières précieuses telles que des monomères, des oligomères ou des mélanges de fractions d’hydrocarbures, même à partir de mélanges de polymères fortement contaminés. Leur composition est très proche de celle des matières premières fossiles et elles peuvent être réutilisées pour la production de carburants ou de plastiques. Dans les processus relativement « robustes », tels que la pyrolyse ou l’hydrocraquage, les chaînes de polymères sont brisées sous l’action de la pression, de la chaleur et des catalyseurs. Dans la plupart des cas, il en résulte un mélange de différents fragments moléculaires. À partir de ce « pétrole brut artificiel », les entreprises produisent des fractions qui peuvent être utilisées comme combustibles ou, comme la fraction de pétrole brut naphta, qui peuvent être réintroduites dans la chaîne de traitement relativement en amont. La solvolyse, qui se déroule dans des conditions douces, utilise des solvants pour séparer les impuretés et les plastiques mélangés les uns des autres, ce qui permet d’obtenir des produits plus purs. Comme dans le cas du recyclage mécanique, les longues chaînes de polymères peuvent être conservées. L’accent est actuellement mis sur de nouveaux procédés qui fonctionnent soit par catalyse classique, soit par biocatalyse, soit par photocatalyse, et qui peuvent donc fonctionner dans des conditions encore plus douces. C’est un avantage en termes de bilan énergétique, mais également en termes de gamme de produits. Dans l’idéal, les monomères individuels des déchets plastiques recyclés peuvent être récupérés de manière très ciblée et réintroduits dans le processus de polymérisation en tant que fraction « drop-in ».
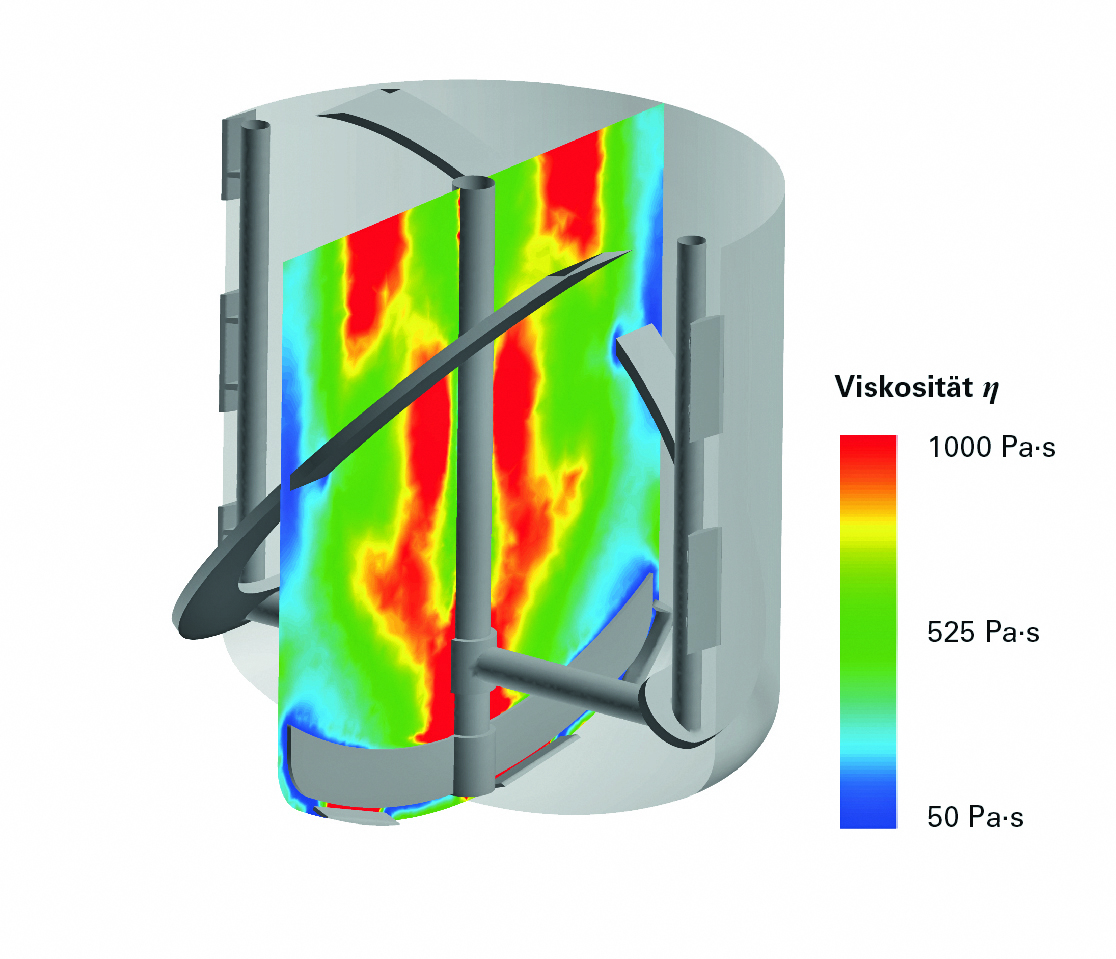
Les défis fondamentaux du processus de recyclage des plastiques
Lors de la première étape, le matériau d’entrée pour la dissolution ou la fusion doit être préparé de manière à fonctionner sans problème et à obtenir un résultat reproductible. En raison de la nature parfois très variable des déchets plastiques, c’est précisément là que réside le premier défi majeur du processus. Non seulement la qualité et la pureté du matériau d’entrée varient généralement significativement, mais des paramètres importants comme la densité apparente, la distribution de la taille des particules ou la mouillabilité du matériau de départ jouent également un rôle décisif. En fonction du processus, il faut s’attendre à des viscosités très élevées, ou même à des défis rhéologiques plus importants, tels que les limites d’élasticité. Dans des milieux aussi exigeants, les process habituels de mélange tels que l’homogénéisation et la suspension, mais également le transfert de chaleur, doivent fonctionner de manière fiable. Une technologie d’agitation élaborée et efficace est donc nécessaire pour homogénéiser la masse initiale et l’amener à la température de traitement requise dans le réacteur.
Les solutions de mélange
Pour les produits à haute viscosité, on utilise généralement des systèmes de mélange à proche de la paroi et à mélange forcé. Il est en effet important de garantir un temps de mélange le plus court possible dans la zone d’écoulement laminaire. Traditionnellement, il s’agit souvent de systèmes à vis hélicoïdale ou à ancre. Les systèmes de mélange modernes tels que l’Ekato Paravisc ou le Paraseg permettent d’obtenir des temps de mélange sur toute la plage de viscosité qu’un agitateur à ancre ne peut pas atteindre en raison de son mode de fonctionnement purement tangentiel.
Avec l’Ekato Paravisc, le mélange axial est obtenu grâce à la forme et à la disposition uniques des deux pales principales. En fonction de l’application, cet agitateur peut fonctionner aussi bien vers le haut que vers le bas. Ainsi, s’il fonctionne vers le bas, le fluide est pressé le long de la paroi, change de direction de mouvement sur le fond et s’écoule vers la surface dans la zone de l’arbre de l’agitateur. Du centre de la surface, le fluide se déplace vers la zone du bord pour être à nouveau tiré vers le bas par les pales de l’hélice. Cela garantit que tous les points de la cuve sont mélangés et qu’aucune zone morte n’apparait. Avec cette hélice, l’introduction du cisaillement est maximale dans l’espace entre la paroi de la cuve et l’agitateur. C’est également à cet endroit que la dissipation d’énergie est la plus importante. Pour les procédés discontinus dont la viscosité varie fortement, l’Ekato Paravisc peut aussi être équipé de chicanes internes afin de fournir une puissance suffisante, même à faible viscosité. Une ancre de fond assure l’homogénéisation dans la zone de fond et la vidange contrôlée du produit. L’ekato Paravisc est utilisé comme agitateur à cadre dans un système d’agitation à plusieurs arbres, ou coaxial pour les produits rhéofluidifiants à limite d’élasticité prononcée ou les suspen-sions à faible teneur en liquide. Il est ainsi choisi notamment pour l’homogénéisation ou pour améliorer le transfert de chaleur.
L’Ekato Paraseg est un autre agitateur destiné aux procédés à haute viscosité. Contrairement au Paravisc, les segments extérieurs des pales sont reliés à l’arbre de l’agitateur. Bien que cette configuration élimine la possibilité d’installer une contre pale interne ou d’autres dispositifs entre les pales et l’arbre, l’avantage d’une homogénéisation rapide dans la zone d’écoulement laminaire est largement conservé et reste nettement supérieure à la performance d’une ancre. Ainsi, L’Ekato Paraseg, certes moins souple d’utilisation que le Paravisc, représente une alternative plus économique pour l’homogénéisation des produits de moyenne à haute viscosité.
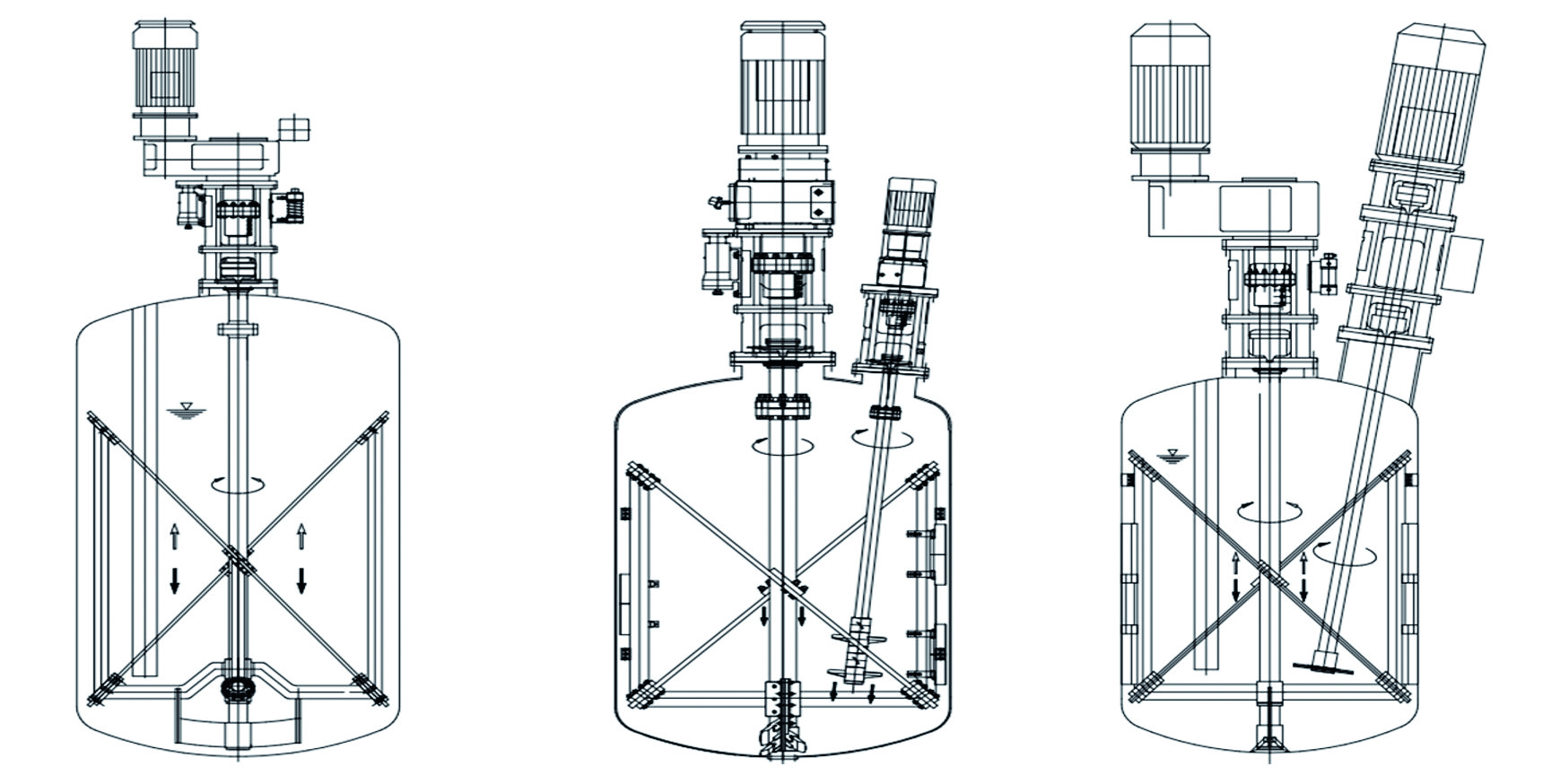
Des réacteurs sur mesure
Pour certains process de recyclage chimique, tels que les procédés thermiques fonctionnant avec des mélanges de polymères, ou les procédés de recyclage du PET, certains procédés sont déjà établis bien au-delà de l’échelle pilote. Certains procédés à base de solvants (solvolyse) ainsi que différents procédés catalysés se dirigent peu à peu vers une installation pilote. À ce stade, Ekato propose la conception de réacteur sur mesure. Sur la base d’accords de développement conjoint, des réacteurs sont développés à partir des procédés du client auparavant et mis en œuvre en tant que système modulaire évolutif à l’échelle pilote. Ekato soutient les entreprises innovan tes dans le développement de technologies de dépolymérisation grâce à son savoir-faire et à son expertise en matière de mélange et de technologie des réacteurs. Les processus impliquant différents types de déchets plastiques peuvent être testés et optimisés dans des conditions réalistes à l’échelle technique au sein du centre technologique d’Ekato ou dans des installations pilotes adaptées au processus spécifique de chaque client. Selon les résultats des essais pilotes, Ekato développe un système de réacteur spécifique. Les outils d’ingénierie (CFD et FEM) sont utilisés pour résoudre les problèmes d’ingénierie complexes, décider des design et valider les solutions optimales les plus rapides, avant même que le réacteur de dépolymérisation ne soit construit. Fort de son savoir-faire en matière de processus et d’ingénierie, Ekato offre des solutions personnalisées pour les process de dépolymérisation, toujours adaptées au processus et aux conditions d’exploitation spécifiques du client. Ekato peut en effet proposer des systèmes de réacteurs à haute température pour la dépolymérisation thermochimique : pyrolyse ; craquage et dépolymérisation thermiques; décomposition catalytique ; hydrocraquage. Ekato peut également concevoir des systèmes de réacteurs pour la dépolymérisation à base de solvants : l’alcoolisation ; hydrolyse ; ammonolyse ; photocatalytique.
À retenir
Pour parvenir à une « économie circulaire » dans le secteur des matières plastiques, les processus de recyclage chimique doivent être mis en place à grande échelle. Ekato déve-loppe et fournit des solutions de réacteurs industriels sur mesure, adaptées de manière optimale au processus de recyclage chimique du client. Cela s’applique non seulement aux processus de recyclage chimique, mais aussi à la production de monomères et de polymères biosourcés et biodégradables. L’optimisation et la conception des procédés, l’ingénierie et la livraison des unités de réacteurs modulaires (skids) sont assurées par une seule et même source, sans interfaces
complexes.