REUSE
L’inauguration du démonstrateur de réutilisation des eaux de process Life Zeus s’est déroulée le 8 octobre dernier, à l’usine de Monin située à Bourges (18). Ludovic Lanouguère revient sur la genèse de ce projet d’envergure avant de nous présenter l’installation et les objectifs à atteindre.
Pouvez-vous présenter les activités de Monin ?
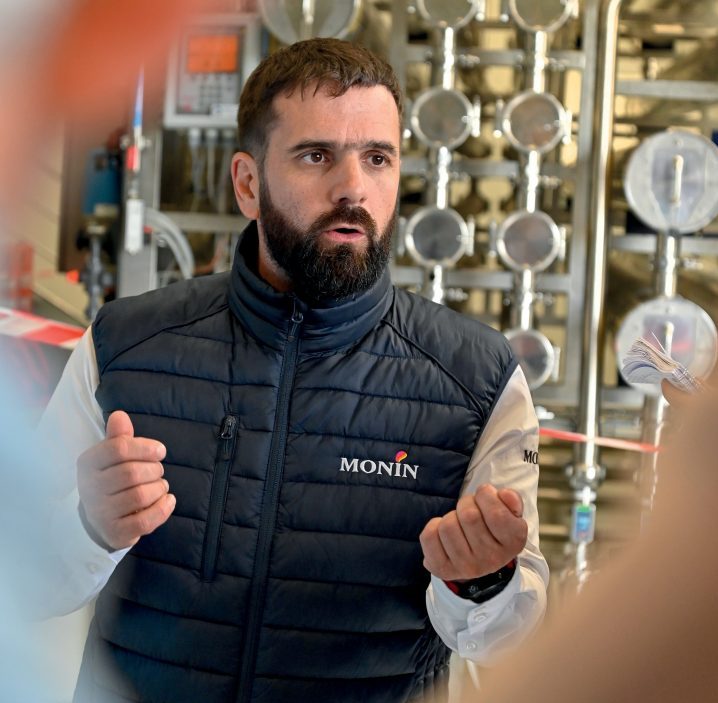
Ludovic Lanouguère : La société Monin est spécialisée dans la fabrication et la commercialisation de produits à destination des professionnels du bar et de la restauration. Nous retrouvons principalement dans notre gamme des sirops, mais nous proposons aussi d’autres produits pour les applications du secteur : mix de fruits, sauces, concentrés, poudres pour frappés, etc. Il s’agit d’une société familiale dirigée par notre P.-D.G. Olivier Monin et qui rassemble près de 1 200 collaborateurs. Nous disposons de huit sites industriels à travers le monde et nous réalisons un chiffre d’affaires annuel d’environ 600 millions d’euros. Nous avons un positionnement premium et fournissons des produits et un service de qualité.
Pourquoi avoir conçu une nouvelle usine à Bourges en 2015 ?
L. L. : Cela faisait plus de 100 ans que le site historique de Bourges était situé au coeur de la ville. Cette implantation a progressivement généré de lourdes contraintes. Les canalisations étaient sous-dimensionnées pour nos volumes d’eaux usées industrielles et la logistique était devenue très compliquée pour assurer les réceptions et les expéditions. En 2014, Olivier Monin avait donc pris la décision de quitter le centre-ville de Bourges et de créer une nouvelle usine, qu’il imaginait propre avec un objectif zéro rejet liquide, ce qui était visionnaire à l’époque. La construction du nouveau site a débuté en juin 2015 et la première bouteille commercialisable est sortie de l’usine en août 2016. Nous avons commencé à travailler sur la question de l’eau en 2019, après une phase de réadaptation dans la nouvelle usine, mais nous ne partions pas d’une feuille blanche. En effet, dès la conception de l’usine, nous avions pris en compte notre objectif zéro rejet liquide et nous avions ré-imaginé notre process de production pour assurer des économies d’eau et éviter les pertes : objectif atteint puisque nous ne rejetons rien dans le milieu naturel et que nous avons d’excellents ratios de consommation d’eau. La société Monin n’a toutefois pas voulu s’arrêter là. Elle a réfléchi à la solution la plus ambitieuse et la plus intéressante possible : réutiliser l’eau dans l’usine. Le projet zéro rejet s’est ainsi métamorphosé en projet de réutilisation des effluents industriels après traitement. La philosophie de Monin ? Avoir de grandes ambitions, se donner le droit à l’erreur et y aller à fond !
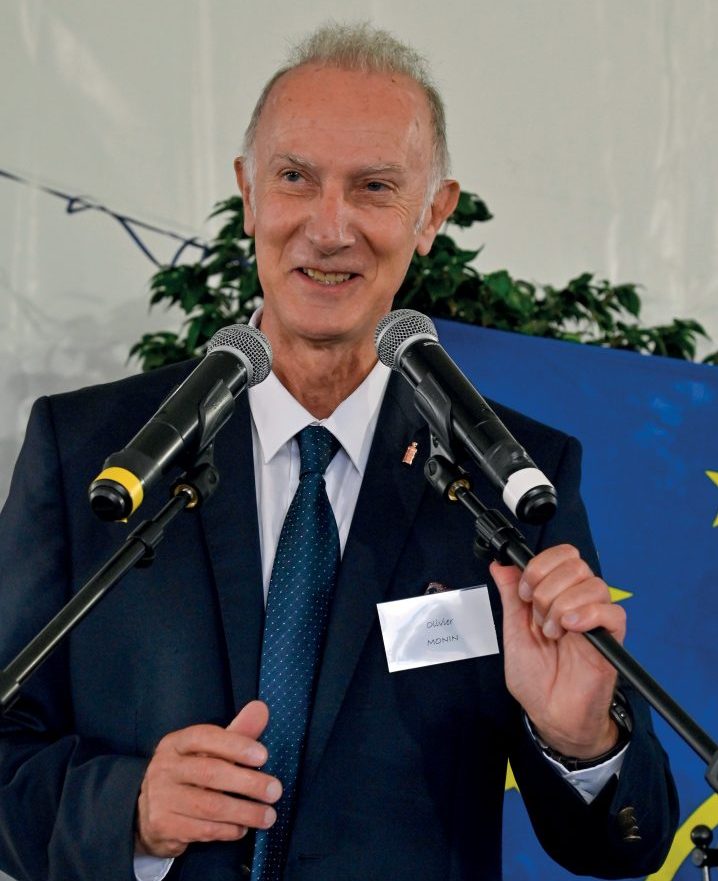
Quels sont les postes de l’usine les plus consommateurs en eau ?
L. L. : Tout d’abord, pour définir s’il était possible ou non d’atteindre l’objectif zéro rejet en réutilisant l’eau dans le process, nous nous sommes penchés sur les grands postes de consommation d’eau sur le site de Bourges. 20 % de l’eau consommée est utilisée comme eau ingrédient et se retrouve dans la bouteille, tandis que 80 % de l’eau consommée est utilisée comme eaux de process, notamment pour les opérations de nettoyage en place. Autrement dit, 80 % de l’eau doit être traitée et rejetée. Notre stratégie est simple : l’eau du réseau de ville va servir d’eau ingrédient et compenser les pertes de notre boucle de réutilisation. La réutilisation d’eau se fera sur tous les usages process. Il ne s’agit pas d’un simple projet de traitement des eaux usées, mais d’un ambitieux projet de R&D.
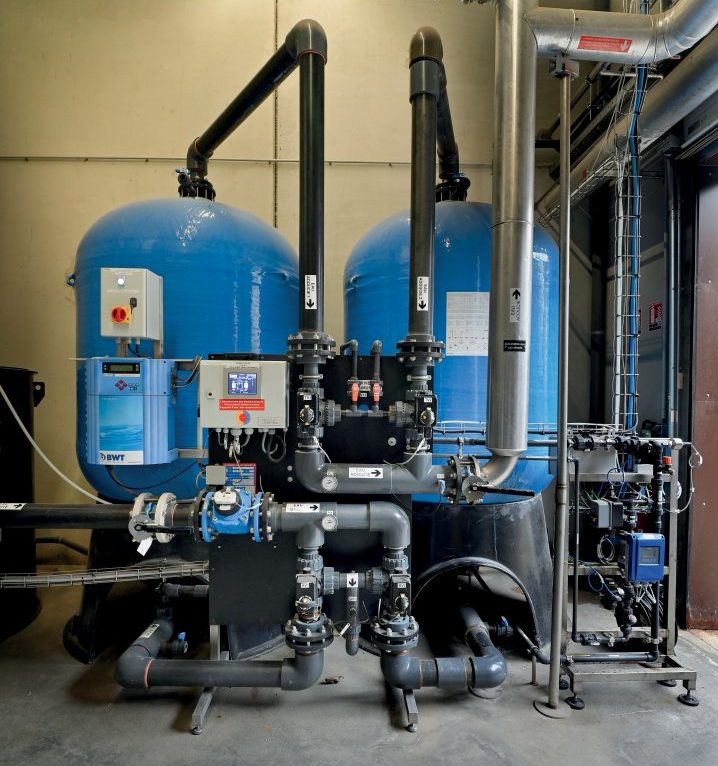
Quel cadre réglementaire s’appliquait en 2019 ?
L. L. : Après avoir défini notre plan de bataille, il a fallu comprendre et appréhender la réglementation en vigueur. À l’époque, en 2019, l’article L1322-14 du Code de santé publique explique que dans le secteur agroalimentaire, il est possible d’utiliser des eaux non conventionnelles si l’on peut prouver qu’elles n’ont pas d’impact sur la salubrité du produit fini ou sur la santé de l’usager. Nous avions interrogé le ministère de la Santé via France Expérimentation, qui nous avait précisé en 2020 que notre projet pouvait être réalisable malgré l’absence de réglementation. Pendant cinq ans, nous avons donc travaillé sans visibilité réglementaire, en essayant d’anticiper les prochaines évolutions. Nous avons pris le risque que notre projet ne puisse finalement pas aboutir. L’ANIA et les représentants des différents syndicats du secteur agroalimentaire ont travaillé à la rédaction des textes, et certaines de nos préconisations ont d’ailleurs été bien prises en compte. Aujourd’hui, la réglementation est adaptée au besoin et à la diversité des pratiques de l’agroalimentaire. Elle prend en compte les spécificités de chaque usine et retient le principe de l’analyse de risque.
Quelle technologie avez-vous retenue et pourquoi ?
L. L. : Nous avons bien entendu comparé les meilleures technologies disponibles sur le marché, comprenant la méthanisation, l’osmose inverse ou encore les boues activées. Nous avons travaillé avec l’Office International de l’Eau et les CRITT de l’INSA de Toulouse, et nous nous sommes demandé s’il n’y avait pas un autre moyen que de réaliser un traitement biologique qui, par nature, dégrade la qualité intrinsèque de l’eau. Plutôt que de dépenser de l’énergie pour dégrader ou transformer la DCO en boues, nous avons imaginé utiliser l’énergie pour séparer et valoriser la matière afin de produire rapidement de l’eau apte au contact alimentaire. Nous avons alors retenu les solutions de filtration membranaire. Un autre détail a son intérêt : nous disposions des compétences nécessaires en interne pour exploiter ce type d’installation.
Pourquoi les essais en laboratoire ont-ils été importants ?
L. L. : Il existe aujourd’hui très peu de documents bibliographiques sur les traitements d’effluents biologiquement instables par filtration membranaire. Nous avons alors signé une convention de recherche avec l’INSA de Toulouse pour réaliser des essais en laboratoire et s’assurer que les membranes étaient capables de produire une eau apte au contact alimentaire. Après un an d’essais en laboratoire et un an d’essais pilotes nous avons pu confirmer les performances de la technologie et s’assurer qu’elles étaient transposables à l’échelle industrielle. Nous avons ensuite intégré au groupe de discussion un fournisseur expérimenté dans le Reuse : notre partenaire Chemdoc Water Technologies. S’en est suivie une période d’essai pilote d’un an sur site, durant laquelle nous avons beaucoup expérimenté. À l’issue de cette période, nous étions à peu près certains de pouvoir produire une bonne qualité de l’eau, à des performances énergétiques acceptables, avec une installation gérable en termes d’encrassement et de colmatage. Nous avons pu définir le schéma général du design de l’installation à mettre en place.
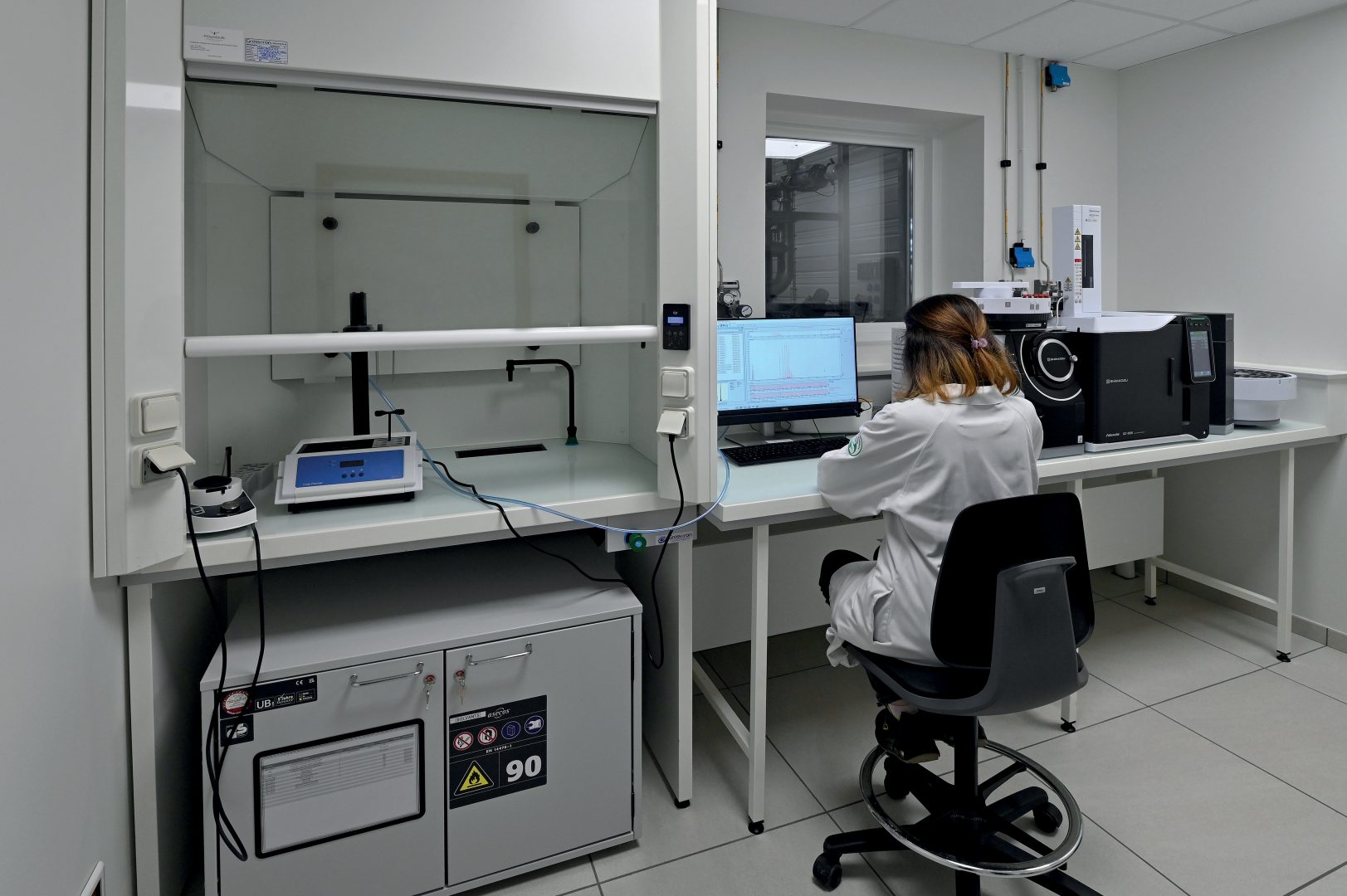
Pouvez-vous présenter les budgets attribués au projet Life Zeus ?
L. L. : Durant nos phases d’essais, les acteurs du projet ont naturellement créé un consortium, composé de Monin, Chemdoc Water Technologies, l’Office International de l’Eau et l’INSA Toulouse. Nous avons eu l’opportunité de répondre à un appel à projets européen, ce qui nous a permis de financer des actions que nous n’aurions pas pu mener si nous avions été seuls à financer le projet. Nous pouvons aller plus loin dans la qualification de l’installation, dans son fonctionnement et sa compréhension, dans le monitoring de la qualité de l’eau, dans la modélisation, etc. En ce qui concerne Monin, le budget attribué au projet Life Zeus est de 4,5 millions d’euros, dont 1,8 M€ subventionné par l’Europe via son programme LIFE et l’Agence de l’eau Loire-Bretagne. Le budget européen attribué au projet est, lui, de 4 M€, tous partenaires confondus.
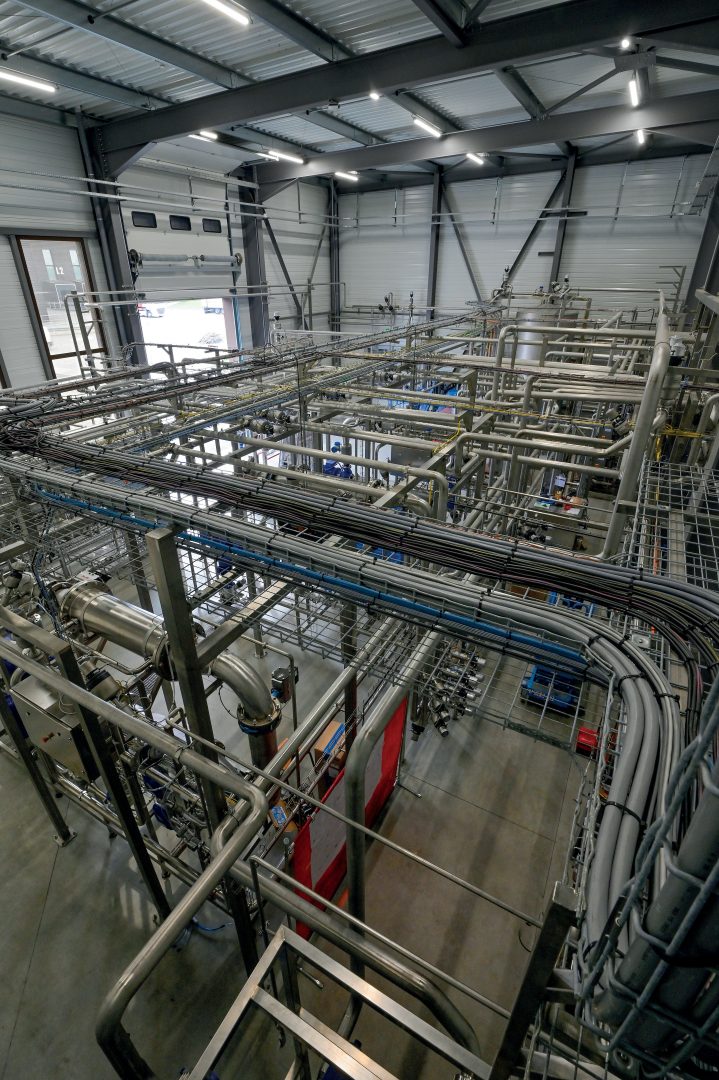
Comment se déroule la mise en œuvre du projet Life Zeus ?
L. L. : Sur le site de Bourges, nous avons d’abord dû réaliser la construction d’un nouveau bâtiment pour accueillir l’installation de Reuse. Nous avons ensuite démarré l’installation fin mai 2024, après avoir réalisé tous les tests techniques, électriques et hydrauliques. La mise en service de l’installation a été réalisée le 8 octobre dernier, le jour de l’inauguration. Pour le moment, nous sommes dans la phase de production d’eau : reste ensuite à renvoyer cette eau dans le process. Nous entrons désormais dans une phase de qualification, de fiabilisation et de surveillance de l’installation. Nous ne pouvons pas nous permettre de non-conformités, nous devons être capables de reproduire les performances. Nous n’avons pas fixé de délai précis, mais nous pensons pouvoir ouvrir la vanne d’ici le 2nd semestre 2025.
Quelles sont les performances attendues ?
L. L. : En 2023, l’usine de Bourges a consommé 54 000 m3 d’eau et en a rejeté 38 000 m3. Avec un rendement supérieur à 80 %, nous espérons renvoyer 30 000 m3 par an dans l’usine, ce qui conduirait à plus de 60 % d’économie d’eau. Sur site, nous avons mis en place deux prototypes de filtration membranaire. Le prototype ReGeCycle est utilisé pour le traitement spécifique des flux salins d’adoucisseurs en vue de réutiliser les saumures concentrées en substitution du sel. L’installation est modeste en termes de taille, mais elle a un potentiel de réplication énorme. Parallèlement, le prototype R-Oasys est utilisé pour le traitement des flux organiques et met en oeuvre une membrane de MF, conçue dans un matériau éprouvé et fiable mais jamais utilisé dans cette configuration ; une membrane de nanofiltration basse pression permettant un traitement efficace des effluents sucrés ; et un traitement de finition de l’eau par osmose inverse.
Quel est le bilan énergétique de l’installation ?
L. L. : Le bilan énergétique de l’installation, toutes énergies confondues sur l’intégralité du cycle de l’eau, du pompage au transport en passant par la distribution, le traitement ou encore la montée en température, est le suivant : lorsque nous rejetons un mètre cube à l’égout, il coûte 20 kW au total. Demain, quand nous traiterons un mètre cube, il rapportera 10 kW : ce gain énergétique est principalement lié à la valorisation des concentrats en méthanisation. Nous gagnerons aussi en énergie du fait que nous recyclerons 30 000 m3 d’eau tiède à environ 28 °C, contrairement à une eau consommée à 15 °C. Pour le site de Monin, le bilan carbone est très bon.
Quid des concentrats ?
L. L. : Dans l’usine de Bourges, l’énergie est dépensée pour concentrer la DCO, ce qui permet de la transporter et de la valoriser en méthanisation. Nous avons signé un contrat avec un méthaniseur très intéressé par le sucre des concentrats. Dans le bilan général du projet, nous avons donc une revalorisation de 100 % de la charge organique, une revalorisation de 100 % du volume d’eau et un recyclage de 65 % du sel. Nos bilans restent provisoires, mais nous sommes très confiants sur la véracité de ces chiffres. La technologie membranaire à l’avantage d’être très reproductible.
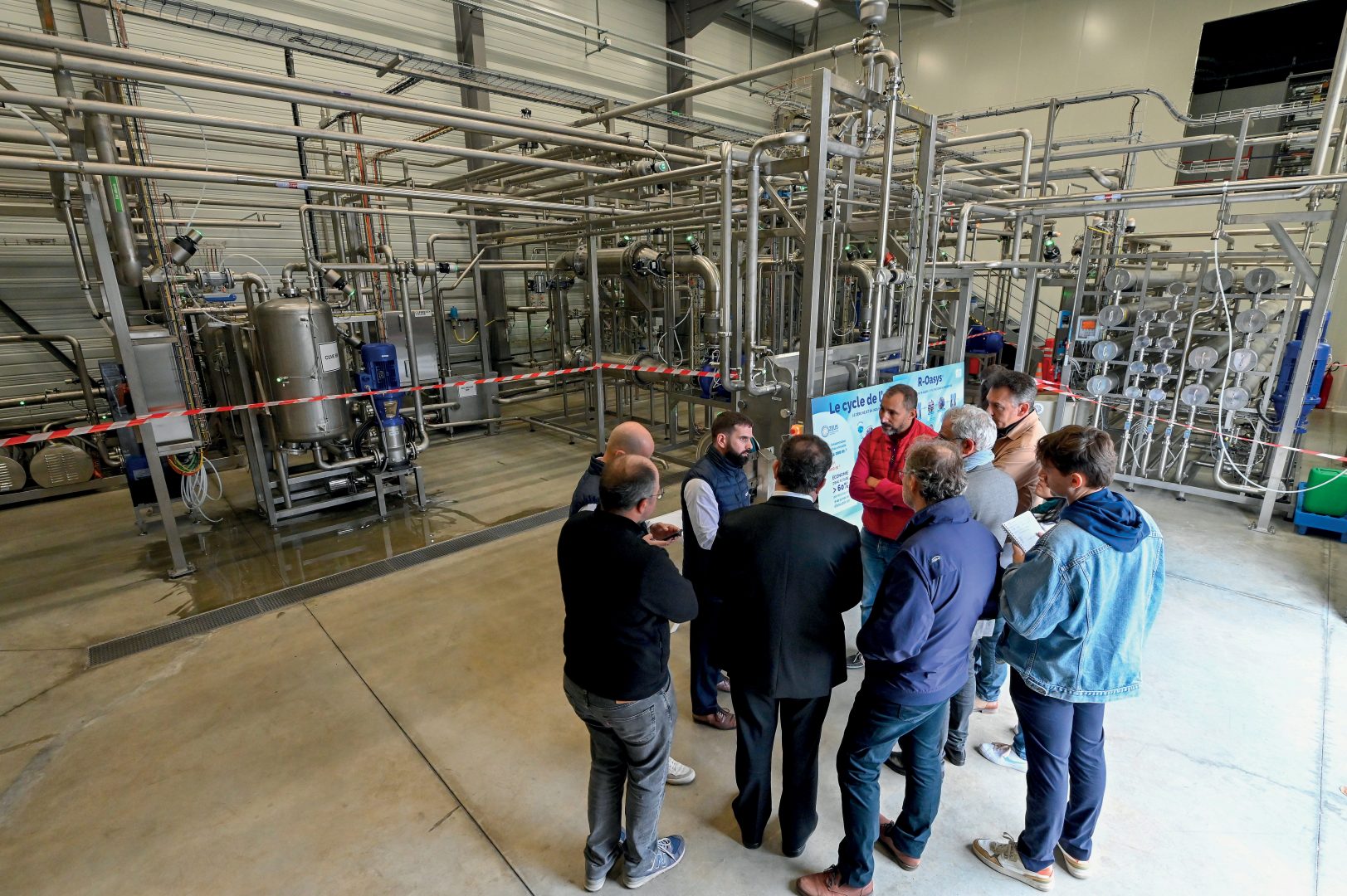
Comment s’est déroulée la journée d’inauguration organisée le 8 octobre dernier ?
L. L. : À l’occasion de l’inauguration du démonstrateur, nous avons accueilli sur notre site de Bourges les cofinanceurs du projet, nos partenaires, nos fournisseurs, mais aussi les élus locaux. Nous avons de la chance que le projet soit très intégré dans le territoire. La communauté de communes de Bourges a beaucoup anticipé et est très dynamique dans la préservation de la ressource en eau. Nous avons pu profiter d’un climat politique et administratif favorable. L’événement a aussi rassemblé les salariés et amis, qui ont pu célébrer la réussite de ce projet. Quelques discours, le traditionnel coupé de ruban et des visites de l’installation de traitement ont été proposés au cours de la journée.