Après l’incendie de son site de production, Copak – concepteur, formulateur et fabricant de produits d’hygiène et d’entretien – a dû se tourner vers un partenaire capable de rééquiper en totalité son atelier de mélange. Compte tenu de l’étendue de sa gamme, Joffe Agitateurs a pu répondre au cahier des charges pour l’ensemble des cuves agitées.
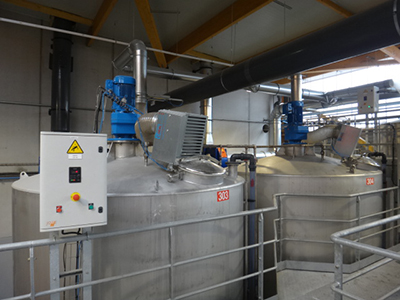
Pour équiper son nouvel atelier, Copak devait trouver un partenaire capable de délivrer des solutions en délais très courts adaptées à la diversité des produits formulés. Plus de 1 000 formules ont été brevetées par Copak et la nouvelle usine offre une capacité de mélange portée à plus de 100 m3. Le mélange implique une analyse précise de l’ensemble des paramètres dynamiques du matériel, comme la vitesse, le design, les pales, les hélices ou encore les cuves, mais aussi des fluides concernés, comme la rhéologie ou la viscosité. Compte tenu de la grande diversité des formules et des volumes à traiter, le défi était de définir des appareils polyvalents, capables d’accepter une large gamme de viscosités et pouvant travailler quelque soit le coefficient de remplissage de la cuve, avec un minimum de 10 % du volume total.
Équipement des cuves
Pour l’équipement de deux cuves de 20 m3 inox 316L, avec un minimum de 2 000 litres, destinées à la fabrication de détergents dont la viscosité peut varier de 1 000 à 5 000 centipoises, Joffe Agitateurs a préconisé l’utilisation d’un appareil type ALN 1000 P combinant deux profils d’hélice ayant chacune une action différente en fonction de sa vitesse de rotation. Ce modèle peut être fabriqué pour des cuves allant jusqu’à 150 m3 et des diamètres d’hélice de 2 mètres. Les cuves de 12 m3 en PEHD prévues pour la formulation de produits corrosifs ont été équipées d’agitateurs AL 800 P. La nature des fluides concernés a nécessité le choix d’un matériau de revêtement spécifique INERTEF de forte épaisseur sur les ensembles arbre-hélices soudés. Tous ces appareils, pouvant travailler efficacement à faible volume sont également étudiés pour tourner sans liquide, lorsque le produit doit être maintenu en agitation pendant toute la durée du transfert ou du conditionnement. Les agitateurs sont tous équipés de variateur de fréquence et les moteurs utilisés répondent systématiquement à la norme IE3 dans le souci d’optimiser les consommations énergétiques.
Produits formulés visqueux et abrasifs
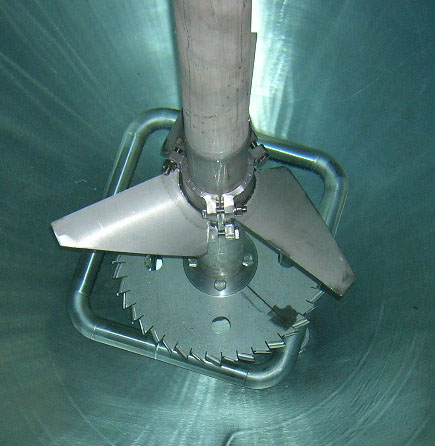
Le second projet a fait appel à une toute autre technologie, les produits formulés pouvant atteindre des viscosités élevées et le process incluant la mise en émulsion de cires et l’incorporation de poudres abrasives dans de fortes proportions. Ces formulations sont, dans la plupart des cas, réalisées à chaud. Les deux cuves, de 500 litres de volume utile, sont équipées d’un groupe thermorégulateur commun, permettant le chauffage ou le refroidissement suivant une consigne déterminée par l’opérateur. Elles sont équipées de disperseurs à vitesse variable munis d’un couple hélice-turbine. L’action combinée d’une hélice tripale à profil mince et d’une turbine défloculeuse permet à la fois un taux de cisaillement élevé nécessaire à la dispersion des pulvérulents, à la formation d’une émulsion ainsi que l’homogénéisation totale du mélange. En effet le profil de l’hélice type P engendre un débit traversant important venant alimenter la turbine défloculeuse type D ayant, elle, une action radiale. Ce couple hélice-turbine est utilisé avec succès dans de nombreuses autres applications comme par exemple la dispersion de pigments ou le broyage des bulbes d’iris dans les process de distillation.
À lire dans le Journal des Fluides n°76 Octobre/Novembre 2016