Dans les installations de fermentation, on utilise généralement des turbines à disques à plusieurs étages pour l’agitation des liquides. Ce procédé établi a cependant quelques inconvénients. Afin de limiter la perte de produits à très haute valeur ajoutée, la société Ekato a développé un tout nouveau système, offrant à la microbiologie industrielle de nombreux avantages en termes de techniques de procédés. Présentation par Klaus Gezork, directeur de projet ingénierie des applications chez Ekato, et Werner Himmelsbach, directeur recherche, développement et ingénierie.
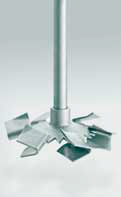
Les procédés de fermentation permettent de générer des composants tels qu’enzymes, principes actifs pharmaceutiques, acides aminés ou vitamines en tant que produits du métabolisme de différents micro-organismes. Pour améliorer la productivité de ces processus, il est impératif de fournir à ces micro-organismes l’oxygène et les éléments nutritifs en quantité suffisante et constante. De plus, les sous-produits du métabolisme, comme le dioxyde de carbone, doivent être évacués, et des conditions idéales de température et d´acidité doivent être maintenues. Pour réaliser des économies d’échelle, on a recours à des installations de plus en plus volumineuses. L’homogénéité des paramètres biologiques et le dégagement de chaleur du fermenteur acquièrent alors une importance sans cesse plus grande. Pour évacuer la chaleur métabolique des micro-organismes, le fermenteur doit en règle générale être équipé d’échangeurs de chaleur tubulaires internes nécessaires au refroidissement.
Inconvénients des systèmes de turbines à disques
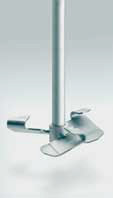
Dans le système de turbines à disques à plusieurs étages utilisé traditionnellement dans le fermenteur industriel, on assiste à une formation « compartimentée », selon laquelle surviennent des défauts d’homogénéité considérables, notamment pour ce qui est de la concentration en oxygène dissous, de la valeur du pH ou de la répartition des éléments nutritifs, ce qui a des répercussions négatives sur la productivité. Le second inconvénient est la forte baisse de puissance hydraulique de la turbine à disques sous aération. Le moteur doit être dimensionné en fonction de la puissance nécessaire dans le cas d’une utilisation sans aération, ce qui génère des dispositifs de sécurité mécanique inutiles et par conséquent des coûts. L’autre solution consiste à prévoir un variateur de fréquence ou un moteur à changement de polarité. À vitesse constante, la puissance absorbée se modifie lorsque les débits d’air changent pendant la durée du batch. Par conséquent, un dimensionnement optimal est difficile. Aussi, quand les débits d’air augmentent, on assiste rapidement, avec les turbines à disques, à ce que l’on appelle un point d’engorgement, au-delà duquel l’air n’est plus entièrement dispersé. Celui-ci monte alors le long de l’arbre en bulles relativement grandes, ce qui peut provoquer une alimentation insuffisante en oxygène des micro-organismes.
La solution développée par Ekato
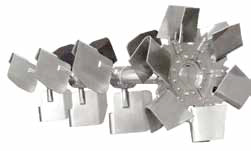
Compte tenu des inconvénients générés par les systèmes d’agitation traditionnels, Ekato a développé une nouvelle solution à partir de ses mobiles d’agitation PhaseJet et CombiJet déjà existants. Ces inconvénients peuvent être réduits au minimum en utilisant un mobile d’agitation primaire à action radiale, le PhaseJet, combiné à un mobile d’agitation secondaire à action axiale. En raison de la très faible perte de puissance sous aération, l’agitateur peut, dans de nombreux cas, être conçu avec une vitesse constante même lors de débits d’air variables : un avantage indéniable en termes de coûts d’investissement. Le CombiJet, comparativement à la turbine à disques, génère des composantes d’écoulement axiales considérablement supérieures, ce qui
permet d’augmenter sensiblement l’homogénéité et par conséquent la productivité des micro-organismes. La limite d’engorgement du PhaseJet est atteinte avec des débits d’air bien supérieurs. Par rapport à la turbine à disques, il offre donc aussi un potentiel d’extension des capacités, en installation neuves ou déjà existantes.
Préserver la sécurité de fonctionnement
Le fermenteur est composé d’un réacteur, d’un agitateur et d’éléments intégrés tels que les chicanes, l’échangeur de chaleur et les dispositifs d’injection de gaz. Lors de la conception du fermenteur, il est impératif de ne pas sous estimer les sollicitations mécaniques. Les conséquences financières de dommages portent certes sur les réparations et les remplacements de pièces, mais la perte de produit et les coûts d’un arrêt de la production peuvent s’avérer plus considérables encore. Seule une vision d’ensemble garantit le fonctionnement sûr d’un système d’agitation. Celle-ci commence par la détermination des forces hydrauliques dynamiques sur les mobiles et les arbres d’agitation, ainsi que sur tous les éléments intégrés. En se basant sur des données de vitesses d’écoulement locales, il est aussi possible d’estimer les fréquences d’excitation sur tous les composants. Ces informations sont alors introduites dans les analyses des éléments finis et les analyses modales, et permettent d’obtenir des données sur les tensions locales dans toutes les pièces critiques et sur leurs fréquences propres. On en déduit les détails de design nécessaires, dernière étape du procédé. La fourniture d’agitateurs et de réacteurs par un fournisseur unique épargne à l’ingénieur en charge de l’installation la coordination des interfaces. Mais plus encore, c’est la seule garantie afin que les contraintes de production et les solutions de design qui en découlent aboutissent à une installation à des coûts abordables et au fonctionnement sûr.